Dubbed the ‘Mecca of heavy metal culture’, the journey to Wacken has become an annual pilgrimage for bands, crew and metalheads alike. This year, TPi’s resident dark lord, Ste Durham, was among them.
Hello, my name is Ste Durham, and I’m a metalaholic. I love blast beats, I love circle pits and I love deafening guitars. As a result of this affliction, I’ve spent the majority of my life revering the legendary Wacken Open Air festival. Essentially the North German location that gives the festival its name is a sleepy little village, home to less that 2,000 people, that’s overrun each year as it hosts what has become the biggest metal event in the world. What began in 1990 as a local festival for a handful of German bands is now an institution: Faster, Harder, and Louder than anything else.
The minute you drive into the village, the festival iconography and eager pilgrims are everywhere, each housing estate and side road teeming with high-vis clad event staff and welcoming locals – many of the latter using the event as an opportunity to sell coffee, beer and other homemade wares from their lawns. Despite what the corpse paint or studded leather may lead you to believe, this is not just a festival, it’s a community.
Wacken is just as impressive from a technical standpoint, with the main double stage (called the True Metal and Black Metal stages) and iconic flaming skull that separates it serving as an imposing centrepiece.
Louder Than Hell
German audio expert Crystal Sound originally came on board to provide sound reinforcement for the 1996 and 1997 incarnations of the festival, before taking a break to focus on other events. The company’s CEO, Gerd Gruss, took up the story: “Following the break, the Wacken promoters saw a 180,000 person event we did and were so impressed that they decided to have us back to supply the main stage audio in 2006.
“We sent out a technical rider to sound engineers for all the leading acts, and in it we proposed to use d&b audiotechnik J-Series for side fills – a system we’d begun to invest in heavily earlier in the year. In Flames’ FOH Engineer Tom Kubik jokingly wrote back and suggested, ‘Hey, why not turn the side fills outward and use them as the main system?’ He admitted later that he’d heard the J-Series on a Slayer tour and had been really impressed. I was already of the opinion that the MOST features of the J-Series (Midrange Outperforms Similar Tops) made this a sensible suggestion, so we polled the other engineers and the promoter about this and an agreement was reached.”
The audio rig implemented across the two main stages at Wacken consisted of four main hangs of 22 d&b audiotechnik J-Series with two outfills of eight J-Series per side. Running along the downstage edge of the True Metal and Black Metal stages stood what must surely have been one of the most imposing sub arrays seen across Europe this summer. The array consisted of 51 sub positions, each of which were made up of two J-INFRAs or three J-SUBs, powered by D80 amplifiers.
This giant audio setup was complemented four delays of 10 J-Series, situated 60 metres back from the main stages and set out to ensure that the 140 metres to the back of the infield area were adequately covered. The system was controlled by d&b audiotechnik R1 remote control software. On-stage monitors consisted of 16 d&b M2’s on the True Metal Stage and 16 M4’s on the Black Metal Stage, both with three d&b D12 amp racks and a Yamaha PM5D for monitor control. Two d&b C7’s with four C7 subwoofers were used on each stage for drumfill, along with two more d&b D12 amplifiers. Sidefills were made up of eight d&b J8’s with six d&b J-SUBs, again with D12 amps.
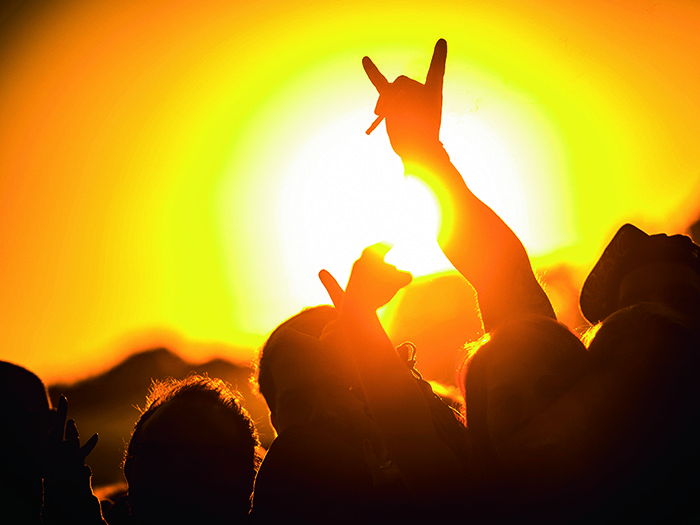
The choice of console at FOH was a Soundcraft Vi6, complete with the requisite stage boxes and stereo equalisers, with TC Electronic and Eventide outboard effects available. The company also supplied a full arsenal of Shure wireless microphones.
Although the True Metal and Black Metal stages could be viewed as two independent performance areas, the shared FOH structure was located dead centre with enough space to house as many as 11 incoming technicians and their desks of choice.
As with many festivals, a big issue for the audio team and the festival promoters themselves is always noise pollution. Although 99.9% of Wacken’s population is fully supportive of becoming the centre of the heavy metal world once a year, there are still the odd one or two that object to having their windows rattled by blast beats and screamed vocals until 3am.
Product Management specialist at d&b audiotechnik, Werner Bayer, was on hand to explain how some of the company’s software developments, both new and not-so-new, were instrumental in the design, rigging and monitoring of the system before and during the festival.
“In 2007, using the d&b ArrayCalc software, we found the algorithms to control the dispersion of the sub array’s low end without compromising sound on site. We have been able to achieve really steep drops above 100° off at each side of the stage, which is an integral part of the system design,” Bayer said. “We worked a lot to keep the noise away from the sides, as well as trying to align the main system and delays so that we can get a higher level of damping at 180° using physical obstructions. It’s all about playing around and running as many simulations as possible to achieve the correct coverage – I firmly believe that the J-Series is still one of the best systems on the planet for this kind of job.”
While the ArrayCalc software was proving useful at successive festivals, the team still striving to have an influence on far field behaviour. Bayer continued: “This is a completely different situation to the first 100 metres, with different physics at work. We partnered in collaboration with noise consulting and software development experts SoundPLAN using our data and their algorithms – the outcome was NoizCalc.”
The software predicts sound propagation of ‘multiple coherently emitting sources’ such as line arrays and subwoofer arrays. Using 3D terrain data NoizCalc accurately predicts the far field noise emission across the terrain according to ISO 9613-2 and Nord 2000 standards, allowing system designers to predict any potential noise issues during the event planning stage.
Gruss continued: “We started doing this kind of thing a few years ago but the rules seem to be getting stricter. The promoter gets his showtimes and, even though we can play until 3am, it is all done under exact guidelines. It is important for us and d&b to know the law and how to find that extra dB for the crowd. It might seem strange to think of the Wacken tagline – Louder Than Hell – and we still have noise restrictions, but that’s the world we live in.”
As well as being able to make use of high-powered software such as NoizCalc and ArrayCalc, Gruss, Bayer and the rest of the audio team were not above using slightly more low-tech methods to achieve their offsite noise-reduction goals. Bayer explained: “The promoter has invested in a number of strategically placed physical obstructions to attempt to dampen the noise even further. In addition, Noise Consultant from AMT, Michael Oehlerking made the suggestion to construct some walls out of straw, as well as more solid structures, to keep the level correct. One of the main structures, a large scaff tower packed with damping materials, can be found at the left side of the Party Stage.”
This stage, set slightly to one side of the double-wide main area, also featured a d&b J-Series system, supplied by Grandpa PA & Light. Bayer commented: “We had some problems with this stage last year, but the J-Series, combined with the new software and physical damping structures, have made our lives here a lot easier.”
The Bullhead City Circus tent, featuring another, albeit smaller, double stage setup, was also supplied by Crystal Sound via dry hire from CGS Licht- und Tontechnik. The company also supplied d&b-manufactured sound reinforcement to additional areas such as the large screens that allowed headline performances to be viewed away from the hustle and bustle of the infield.
The Wacken Experience
The audio crew and incoming engineers shared the space at a two-storey FOH structure with visual technicians, many of whom came from main lighting, rigging and video supplier, PRG XL Video. Although the two main stages started life as an A (True) and B (Black) setup, the promoters and design teams have already begun making the two as equal as can be.
Lighting Designer Jerry Appelt explained: “Although the two stages are becoming more similar, the True Metal stage still has around 20% more kit this year. Basically the main rig is oriented around Iron Maiden’s setup, who headline on Thursday night. It’s a mixture of a functional festival design and what Maiden’s crew needed to make the changeover as comfortable as possible. The Black Metal stage is closer to a usual festival rig – a versatile and familiar setup to make sure all the incoming bands are comfortable and can still have strong looks during the daytime.”
The True Metal rig included 40 Martin by Harman MAC Viper Profiles, 54 Vari-Lite VL3500 Washes, 39 Clay Paky Sharpys, 37 SGM Sixpacks, 24 SGM P5’s, and 42 SGM Q7’s. The design was reinforced by audience blinders, washes and decorative lighting fixtures such as the iconic 18 A&O Falcon 7kW Beams that were mounted on the roof of the stage and used as searchlights.
Appelt continued: “Usually we design both stages independently but Maiden gave us the details so early that we thought it would be quite easy to accommodate. It’s a good flown rig and it allows us to keep the floor as clean as possible, making it simple to accommodate set pieces and floor packages for each band, as well as making for quick changeovers.
“It doesn’t make sense to include a bunch of strange or rare equipment that will throw the LDs off when they receive the kit lists. We always try to provide a mixture of what we want and what PRG can deliver – it is important to stay flexible. There are always add-ons so it’s a give and take relationship.”
The Black Metal stage rig consisted of much the same fixtures, used more sparingly or in slightly different ways. This included 29 Martin by Harman MAC Viper Profiles, 42 Vari-Lite VL3500 Washes, 54 SGM Sixpacks, 24 SGM P5’s and 26 SGM Q7’s. The stage had the exact same quantities and design for its audience blinders, washes and decorative lighting fixtures. Both stages had MA Lighting grandMA2 Full Size desks on hand for the LDs that would rather work from a show file than haul desks 60 metres through the no man’s land that formed between the stages and FOH during the weekend.
Although the design for both of the main stages used modern fixtures, Appelt maintained a reverent view when it came to the heritage of such a visually distinctive genre. He added: “I’m always looking back into the history of metal and that generally means a lot of PARcans and blinders! I don’t want to lose this approach completely, but six lamp bars are simply no longer the appropriate tool, as they are too labour intensive. Setting up beam lights in rows of four is reminiscent of the old ACL four light groups, so this is what I have in mind – always making sure we remember where we are coming from.
“The bottom line was not to create stunning, never-before-seen designs, it was to support the bands in the best possible way. To provide the bandwidth in the rig for them to do the best they can. It’s quite different to other festivals because here, Wacken is the star, not the main act. The people come to have the Wacken experience, and we are in the business of creating the Wacken look. Things like the 7kW searchers on the roof of the stage and the fiery skull – that’s what the people look for and that’s what we try to provide.”
The team opted to use a WYSIWYG system for the seventh year running to allow incoming LDs to fine-tune their shows, situated in the production area behind the two main stages. This ran on the same network as the rest of lighting and video across the festival site, though the multiple layers acted as a buffer just in case. Appelt said: “The performance of WYSIWYG is great. As a tool at a festival of this size it’s very helpful, plus it allows the designers to get away from FOH at night while the crew works on the changeover. It’s really accurate and can achieve a fantastic result if you know how to handle it.”
As well as providing lighting, PRG XL Video also supplied an extensive of amount of video, including LED backdrops for the main stages, three main stage IMAG screens, one IMAG screen mounted on the back of the FOH structure, two at the Party Stage, and one at Bullhead City Circus as well as six LED trucks for information, warnings and showing select band sets. The kit on site varied, though the two main stage setups consisted of identical 18m by 7m backdrops, made up of 30mm panels and controlled by two PRG Mbox EXtreme media servers and two MA Lighting grandMA2 Light consoles.
According to Unger, the lack of space behind the stage was the biggest problem for the LED crew as well as the lighting guys – though they know the site well enough by now to adapt their way of working. He said: “We can only bring in three trucks behind the main stage, one on each dock, so we park our trucks up early and the stage is built around us. We work really closely with the stage management team and have known about these factors for years.”
He continued: “As guests tend to come just as early, we have to have some of the LED trucks ready to go by Monday morning to broadcast information and so on. These techniques are something we’ve developed over the years. They improve things each year at this festival, and that includes making it better from the crew as well as the fans. It’s all about maintaining and improving the quality of the Wacken experience.”
Appelt also gave his view on what the festival’s visual identity is rooted in: “Wacken tries to stay away from a lot of LED like some other festivals. The stage itself and the lighting is more real, and a great deal of work goes on around the site in terms of practical decoration. They make the extra effort to use nice prints or subtle gobo projections on a tent – anything to make people feel at home here and enjoy it. You can also feel this on stage and with the crew. Everybody here tends to see the bigger picture.”
All In The Family
Stageco arrived at Wacken on Sunday 24 July with a three-man team to begin offloading trailers in preparation for the half crew arriving the following day. By the time the full team arrived on Tuesday the total crew including forklift and crane drivers amounted to 98 people. The team built the True Metal, Black Metal and Party Stage, as well as other major structures such as the entrance gates, scaff towers, VIP to infield staircase, FOH structures, and meet and greet area.
Stageco Crew Chief Markus Olma was on site to coordinate this massive endeavour: “We need the maximum time and space to work, that’s why we start a bit earlier with the trucks. We also lift the main stage skull, which is owned, along with the rest of the bespoke décor, by the promoter. Everything we supply is stock, the majority of which has been the same since switched to a four-tower main stage system in 2013 for Rammstein.
The most difficult thing on site is the slope, which is around two metres from left to right. It’s tricky for stage builders but, much like with the famous Wacken weather, we’re used to it. A double stage means double work, double drawings, and double truck space but it’s more or less the same task as any other festival rig.”
At its busiest period during load-out, Stageco had 62 trucks on site, many of which had arrived with gear from the company’s warehouses in Berlin or Belgium, as well as from ongoing European tours. Olma continued: “Sometimes we drive 900km to supply this festival, and in the German summer the main highways have restrictions on trucks at weekends. All of this has to be accounted for during the planning stage – it’s difficult but not too complicated if it is well organised.”
A key figure in Stageco’s engineering department during the planning stage was Kai Eppinger, who was on site to make sure his mountains of blueprints and kit lists were followed to the letter. He said: “Despite the size, all the tasks we have here are quite standard. The biggest roof here is only a 20m system, and even though the rigging capacity is large, there have been no problems this year. Rammsetin in 2013 is our benchmark because that was a much harder show with a lot more space and weight – 35 tonnes of production in the roof alone! There’s a lot of administration and calculations involved, and the authorities have to check structures – I have 10kg of paperwork with me in the production office that took a week to print!”
Due to the sheer size and scale of Stageco’s duties at Wacken, a special crew was assigned to build each of the different components. This involved meticulous detail from Eppinger, supplying colour-coded, separate drawings for each part of each structure. He continued: “Every year the promoter hires a company to designate where each of the structures are to be placed with GPS. The edges of the buildings are marked with little wooden markers in the ground, which are numbered and coloured so we know where to begin.” While the weather in northern Germany was uncharacteristically kind during the festival itself (and the Tuesday of the build in particular), the crew still had to deal with Wacken’s notorious rain – or more specifically what it can do to the ground. Olma was more nonchalant: “When you have a good delivery schedule and a good working plan, the weather doesn’t matter. The job will be done whatever the weather – it’s just a case of whether we’re wearing a jacket or not. Stages are designed to be outside, even near the sea in the north of Germany.
“Everyone is happy when the sun is shining but we just adapt. We have to try and not damage the grass too much before the fans arrive – forklifts and cranes in particular could tear up the infield. We always have a plan B so that we can work elsewhere if the rain is too heavy. We can make pathways from aluminium panels or use tractors that won’t damage the ground too much.”
Eppinger added: “The promoter is from this village so he does not want to cut all of these trees and pour concrete down to make more space behind the stages. It’s a big family here and we want to look after the festival grounds. It works still after all these years and we know what to do.” Although Wacken’s famous double stage system is becoming more popular at festivals the world over, the team has been reluctant to make too many alterations to the layout itself to over the years, limiting the year-on-year changes as much as possible.
Eppinger continued: “We have worked in some new ideas this year but most of them will be invisible to the fans, like the new platforms and new skin systems for the dimmer cities. We still adapt to suggestions. For example, we made the headers for the main stages slightly bigger this year and changed the PA tower as well. It’s generally just small details to make life easier for the tech guys and the fans. We could make an even bigger stage but for emergency exits and trees, neither of which can move.”
Another of the distinctive characteristics of the Wacken main stages is the giant metal cow’s skull that looms above the central IMAG screen and is engulfed in flame once the sun sets. Although pyrotechnics supplier Pyrotec performer GmbH Germany were in charge of providing the fuel and kit to make this effect possible, Olma and his crew were the ones in charge of flying the gargantuan icon into its rightful place: “The pyro is permanently installed within the steel, they just connect the gas lines. We know the pyro guys really well and if they ask us to check things then we will. He trusts us to fly the skull. When the steel company and the pyro guys designed it, we installed two platforms to help – hidden behind and used to fix problems and service pipelines. The lighting and production guys can use it as well to maintain fixtures or cameras.”
Manfred ‘Pyro-Manny’ Weniger, Owner of Pyrotec, has been a part of the Wacken family for the past 20 years, origiannly being brought on to make the promoter’s dream of a flaming skull a reality. He laughed: “They came to me to ask if I could make it appear as if the skull was burning for the duration of the festival, as well as breathing fire at certain points – I just said yes without knowing how I do it! This requires a lot of preparation and careful planning in the weeks and months leading up to the festival. There are many gas lines and ignition cables that have to be laid and then kept on top of, but it always looks very spectacular when you see the it burning in the darkness.”
This year Pyrotec had eight crewmembers on site for a week prior to the event to ensure that the various flamethrowers and other effects were correctly installed. All told, Pyrotec’s kit consumed around 17,000 litres of propane during the festival weekend.
As well as the skull, the company works closely with Stageco to ensure that Wacken’s pyrotechnic armoury is rigged in a timely manner. Weniger said: “For example, we have specially designed our flame projectors so they are adapted to Stageco’s building materials. This makes a quick rig with a crane possible, allowing us to install everything in a short space of time.”
He continued: “It is a heavy metal festival, which means everything must burn, flash and bang as much as possible! Like every year we had to do a lot of work with very little sleep, but it is always done in a way that seems like fun.”
Olma agreed: “It really is like a family here and crew all works together. The two promoters each lunch in the same tent with all the other workers and that level of comfort makes life here easier for everybody. We have all the heads of departments in a meeting at 7am to talk about any issues, meaning we all know what to expect the next day. The production meeting every day is all departments – including the trash guys and traffic control guys – to give and advice they can and share their observations. We all have the same problems and we all know when the show starts – end of story.”
See You Next Year… Rain Or Shine
Tickets for the 2017 edition went on sale before the last trucks rolled out of Wacken, with 50,000 being snapped up in 45 minutes and less than 10,000 available at the time of writing. Very soon, over 75,000 people from all over the world will have spent their hard-earned cash and pledged to return to a tiny village in northern Germany with little to no information about who will be on stage. That’s how important this festival is.
While the residents of Wacken and these fervent fans return to their daily lives, the crew are already preparing to make sure their faith in the festival is repaid – working over the next 12 months to ensure that this famous event remains just as powerful and inspiring, year after year. Long may it continue.
TPi
Photos: Christine Elser, Pep Bonet, Olaf Malzahn
www.wacken.com
www.prg.com
www.crystal-sound.de
www.grandpa.de
www.stageco.com
www.cgs-licht-ton.de