Did you face any challenges bringing this product to the market?
“The biggest challenge to starting fresh is just the time it takes. Normally, when incrementing an existing product it’s just a few months in development, however, the Triton series was 18 months in development as we created new supervisory systems, better sealing, a more compact integrated shutter and more.”
How did you ensure durability while keeping the unit compact and lightweight?
“By keeping the machining of all housing components in house, we’re able to keep tight control of tolerances to ensure all the panels fit together very well. Doing our own machining means that we can spend a little more time on operations like panel lightening that may be cost prohibitive if we were paying for time on someone else’s CNC machines.”
How is Triton designed for easy maintenance or servicing in the field?
“We try to decrease potential points of failure and make the areas users do frequently interact with very rugged. Our remote stop line and data stream are combined into a single EtherCON cable into our integrated EtherStop switch using Neutrik EtherCon TOP connectors. Instead of multiple cables, it’s just one cable and we use premium connectors. The connector interface doesn’t have the switch circuitry on it, so after years of regular use when the connectors do begin to wear, they can be replaced without having to replace the sensitive and expensive circuitry.”
What challenges did you encounter integrating laser control with traditional lighting control protocols?
“Our biggest challenge is the preconceived notions out there of laser control. Some of our biggest advocates of the Mercury firmware were staunchly opposed to DMX control of lasers… until they tried it. Once a lghting designer understands that the profile operates just like a moving head, suddenly they’re able to use their skills and the tools of the lighting desk to produce amazing effects quickly, and the laser feels like it’s just another type of lighting fixture to them from the control standpoint.”
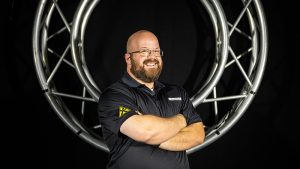
What feedback did you receive from lighting designers and end users?
“Our relationship with our users is built on trust and constructive criticism; we love when they tell us what they don’t like so we can improve it. The first Triton prototypes performed well in the field but the feedback we got was that they needed to be easier to handle and the yoke should be redesigned, so we went back to the drawing board on those items and the end result is a very refined product.”
What safety features have been built into the Triton T Series?
“The Triton Series is all built to be more than compliant with the IEC 60825-1 standard including a Class IV reset system, dual emission indicators, low-profile but visible and durable labelling and an integrated fail-safe shutter system.”
What steps were taken during the design and manufacturing to ensure sustainability?
“One of the huge advantages we have with direct injection diode lasers is they are inherently very low draw for huge impact. A 40W laser system is enough power for a stadium show, but only draws 1,000W at its peak. We take steps to make sure our manufacturing process is as sustainable as possible; nearly the entire housing is made of aluminium and the chips made in the process of machining the housing are recycled.”
Where can we expect to see the Triton T Series in the coming months?
“The Triton Series will expand with new power levels and different housing accessories in the coming months. You can see us at LDI in Las Vegas this December (booth #1885) or visit x-laser.com/pro to learn more, request a demo and get pricing on our full production-grade line-up.”